The natural process of corrosion occurs when materials, particularly metals, wear away as a result of chemical reactions with their surroundings. Iron rusting is the most common type of corrosion.
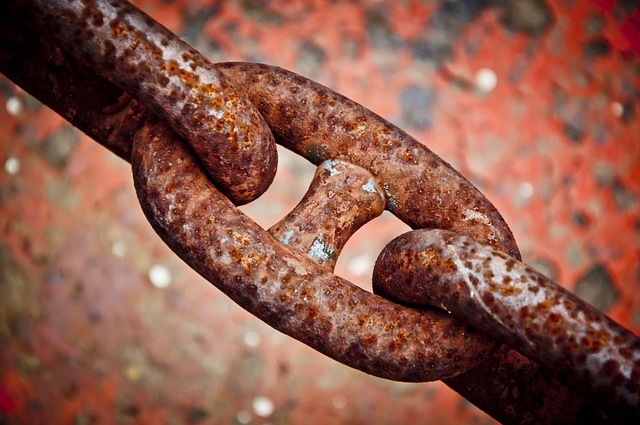
What is Corrosion?
The slow breakdown of metals or alloys due to chemical processes, naturally oxygen, water, or environmental chemicals, is known as corrosion. In most cases, the metal reacts with environmental elements like oxygen, moisture, or acidic molecules to generate oxides, salts, or other compounds. To put it simply, it’s the “decay” of a metal brought on by outside factors.
For example, iron combines with oxygen and water to generate iron oxide, or rust, which weakens the metal and detracts from its strength and beauty.
The slow eating away of metals when exposed to the atmosphere is called corrosion.
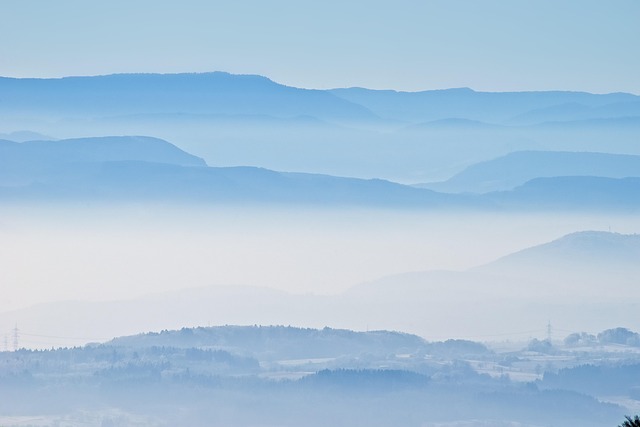
Corrosion of iron (Rusting):- It is an electrochemical phenomenon which occurs in the presence of moisture and oxygen.
At Anode:- 2Fe(aq) — 2Fe2+(aq) + 4e– ; E0 (Fe2+ / Fe) =0.44 V
At Cathode:- O2(g) + 4H+(aq) + 4e– — 2H2O(l) ;E0(H+/ O2 /H2O) = 1.23 V
Overall reaction:- 2Fe(s) + O2(g)+ 4H+(aq) — 2Fe2+(aq) + 2H2O(l); E0(cell) = 1.67 V
Types of Corrosion
Uniform Corrosion:
This is the most common type of corrosion, in which the metal corrodes uniformly across its whole surface.
Because the corrosion happens at a constant pace, it is simpler to anticipate and stop.
Iron rusting in damp air is a common example, when the metal’s surface corrodes uniformly.
Galvanic Corrosion:
This occurs when two distinct metals are in touch with each other in the presence of an electrolyte (such as water).
One metal serves as the cathode, which is protected and the other as the anode, which corrodes.
Connecting a piece of iron to a more noble metal, such as copper, is a classic example. Because the iron loses electrons to the copper, it corrodes
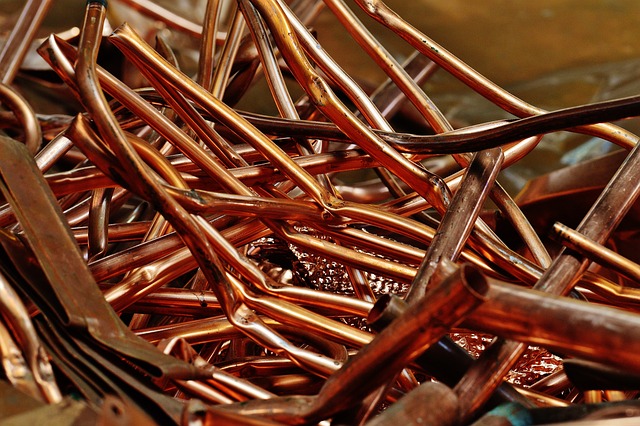
Pitting Corrosion:
The metal surface develops tiny holes or pits as a result of this localised type of corrosion.
Deep pits or holes are frequently seen in stainless steel, where some parts of the metal are more prone to corrosion than others.
Pitting can be dangerous as it might go undiscovered for a long period before the metal eventually collapses.
Intergranular Corrosion:
Occurs along a metal’s grain boundaries and is frequently brought on by the metal’s alloying components or exposure to high temperatures.
It severely compromises the material’s integrity and strength, making it fragile.
Crack Corrosion:
Occurs in small cracks or openings when water and oxygen movement is restricted, changing the electrochemical environment.
Typical in places where air and moisture cannot flow easily, such as bolt holes, joints, or seams.
Factors Influencing Corrosion
Several factors influence how fast and severe corrosion can be:
Oxygen:
Oxygen is essential for the corrosion of metals, especially iron, as it forms iron oxide (rust) when it reacts with iron atoms.
Temperature:
Because of higher temperatures chemical reactions accelerate they usually result in an increase in corrosion rate.
Acidity:
Corrosion is accelerated by acids. For example, hydrochloric acid can rapidly erode metals, but more neutral conditions, pure water, are less aggressive.
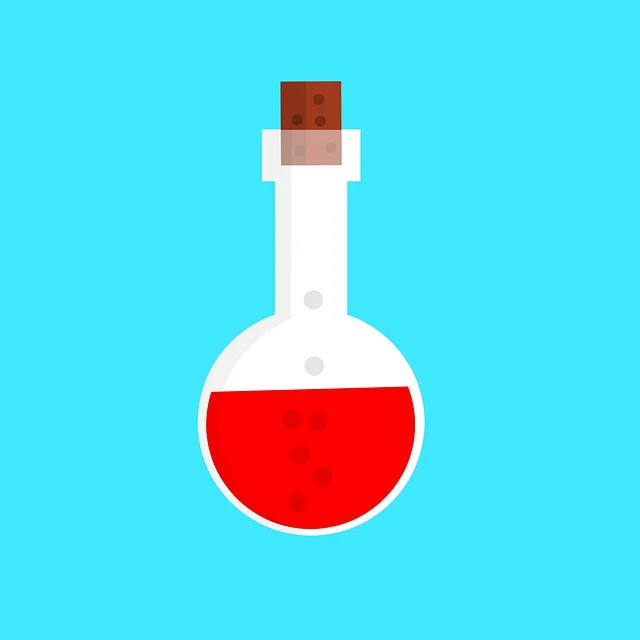
Electrolyte Presence:
Metals that are submerged in salty water or exposed to humid air that contains salt corrode more quickly. Salts (like sodium chloride) act as electrolytes that enhance the metal’s corrosion.
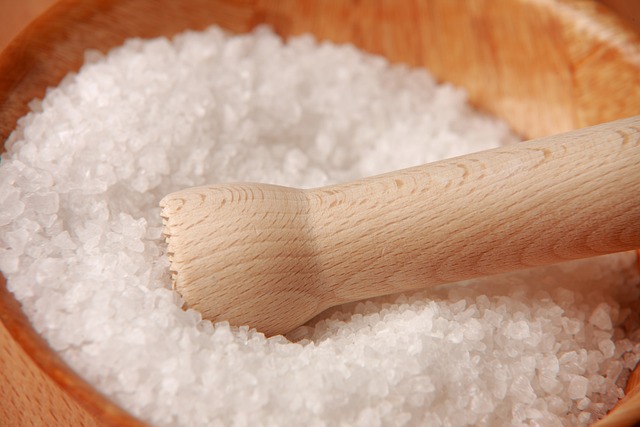
Prevention of Corrosion
Since corrosion is unavoidable, several methods can be used to minimise its impact. These are given below:
Coatings: The metal can avoid direct contact with environmental factors by being covered with a protective coating. Like, painting on iron or galvanizing steel (coating it with zinc) prevents rusting.
Cathodic Protection:This technique requires binding a metal that corrodes more readily, such as magnesium, to the structure that requires defense. To prevent harm to the shielded metal, the sacrificial metal corrodes in its place.
Alloying: Combining of certain metals makes them more corrosion-resistant. Like, stainless steel, which is extremely resistant to rusting, is created when chromium is added to steel.
Method used for prevention of corrosion are barrier protection, sacrificial protection and anti-rust solutions.
Use of Corrosion Inhibitors:
It is possible to slow down the pace of corrosion by adding chemical substances to the surroundings. The electrochemical reactions that take place at the metal surface are slowed down by these inhibitors.
Environmental Control: Corrosion can be avoided in part by limiting exposure to oxygen, moisture, or acids. Corrosion processes can be slowed down like, by utilising sealed containers or controlling humidity levels in particular situations.
Corrosion in Everyday Life
Corrosion impacts daily life and is not limited to industrial metals. Corrosion can harm pipelines, buildings, bridges, and even electrical equipment. The expense of replacing corroded materials, repairing damaged structures, and preventing additional degradation can be very important. Therefore, preventing corrosion is essential for maintaining the integrity of different materials and conserving money.
Hydrogen Economy:-
Hydrogen can be used as renewable and non-polluting source of energy. Water will split to hydrogen and oxygen using solar energy.
2H2O(l) —kv— H2(g) + 1/2 O2(g)
Combination of hydrogen in a fuel cell will produce water.
H2(g) + 1/2 O2(g) — 2H2O(l)
Both these technology are based on electrochemical principles. This production of energy will be very economical in comparison to fossil fuels and nuclear energy.
Summary
Metals are among the many materials that are impacted by the complex process of corrosion. We can reduce corrosion’s harmful consequences by knowing its mechanisms and putting precautionary measures into place.
There are several methods for protecting materials from corrosion, for their longevity and functioning, ranging from the use of coatings and alloys to the application of cathodic protection and environmental control. Preventing corrosion is essential for both practical and safety reasons, whether in everyday objects or industrial applications.
The slow degradation of metals brought on by chemical reactions with environmental elements such as oxygen, water, or acids is known as corrosion. The most common example is when iron rusts, forming iron oxide through a reaction with oxygen and water.
The main types of corrosion include:
Uniform corrosion: Occurs uniformly across the surface.
Galvanic corrosion: Occurs when two different metals are in contact in the presence of an electrolyte.
Pitting corrosion: Localised corrosion forming small pits on the surface.
Crevice corrosion: Occurs in narrow spaces where water or air flow is restricted.
Intergranular corrosion: Affects the grain boundaries of a metal.
The rate of corrosion depends on several factors:
Moisture: Water acts as an electrolyte, speeding up the reaction.
Oxygen: It is effective in most corrosion processes, especially in rusting.
Temperature: Higher temperatures generally increase the rate of corrosion.
Acidity: More acidic conditions accelerate corrosion.
Presence of electrolytes: Salt water or moist air containing salts enhances corrosion.
Rusting of iron is an electrochemical process where iron reacts with water and oxygen to form iron oxide (rust). The reaction can be summarised as:
4Fe + 3O2 + 6H2O → 4Fe(OH)3 → Fe2O3 . xH2O. This rust weakens the iron and reduces its strength and appearance.
Several methods can be used to prevent corrosion:
Coatings: Applying a protective layer such as paint or galvanizing.
Cathodic protection: Using a sacrificial anode to protect the metal.
Alloying: Adding elements like chromium to form corrosion-resistant alloys (e.g., stainless steel).
Use of corrosion inhibitors: Adding chemicals to reduce corrosion rate.
Environmental control: Reducing exposure to moisture and oxygen.