How materials react to forces is the stress-strain curve. Important information about a material’s strength, elasticity, and resistance to external stress is provided by this curve.
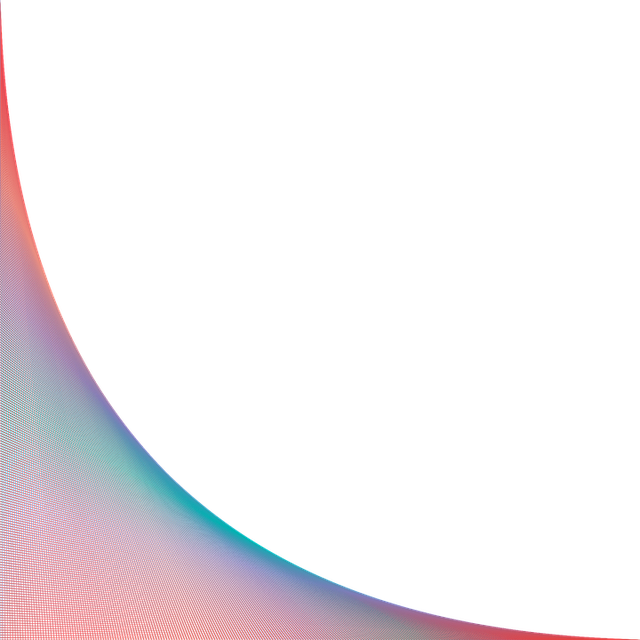
What is Stress and Strain?
1.Stress (σ): It is the internal restoring force per unit area that develops when a material is subjected to an external force. Mathematically,
Stress = Force (F) / Area (A)
The unit of stress is N/m² or Pascal (Pa).
2. Strain (ε): It is the measure of deformation in a material due to applied stress. It is the ratio of change in length to the original length:
Strain = Change in Length (ΔL) / Original Length (L)
Strain is a dimensionless quantity (it has no units).
The Stress-Strain Curve
A material, such as a metal wire, passes through several phases of deformation when force is applied to stretch it. The stress-strain curve is obtained by plotting stress (y-axis) against strain (x-axis). Each of the several zones on the curve represents a separate mechanical behavior of the material.
Elastic after effect: Elastic after effect is the term used to describe the brief delay that occurs when an elastic object regains its configuration after the deforming forces are eliminated.
Elastic fatigue: It is the result of an elastic body’s behavior becoming less elastic due to repeated alternating deforming stresses.
Elastomer: Elastomers are materials that may be stretched to produce significant strains, such as rubber, aortic tissue, etc.
The elastic tissue of the aorta, the major tube (vessel) that carries blood from the heart.

Proportional limit
• The curve’s first straight-line segment.
• In this area, stress and strain are directly related, indicating that the material complies with Hooke’s Law:
σ = E⋅ϵ, where E is the material’s Young’s modulus, a measurement of stiffness.
• The material has elastic behaviour, which means that when the force is released, it will revert to its initial shape.
Elastic Limit:
If further stress is applied, the material experiences persistent deformation and does not fully restore its original shape.
This is the highest stress at which the material can return to its original shape following the removal of stress.
Yield Point:
• The material moves into the phase of plastic deformation after surpassing the elastic limit.
• A small increase in strain results in notable deformation at the upper yield point.
• The material becomes less elastic, which means it won’t regain its previous shape even when the force is removed.
Plastic Deformation
This is vital for manufacturing procedures like forging and metalworking because:
The material expands permanently without breaking;
• It experiences significant deformation with a slight increase in tension.
Ultimate Strength (Maximum Stress Point)
• The material begins to weaken after this point, even when tension is being applied; this is the highest point on the stress-strain curve where the material can sustain the maximum amount of stress before failing.
Necking and Fracture
• The material thins out (necking) after achieving ultimate strength and ultimately fractures.
• The material fails because it can no longer withstand stress.
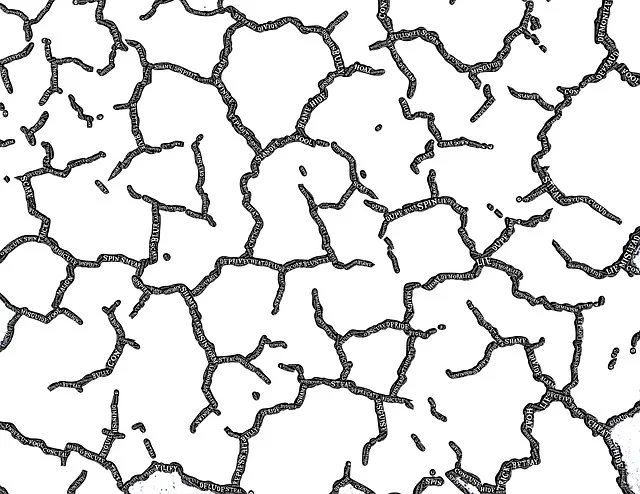
Key Points of Stress-Strain Curve
Hooke’s Law is valid only up to the proportional limit.
Elastic Limit (Point A) defines the boundary between elastic and plastic behavior.
Plastic Deformation is useful in shaping materials without breaking them.
Ultimate Strength is the maximum stress a material can handle.
Breaking Point marks material failure.
Applications of the Stress-Strain Curve
• Engineering and construction: Assists in creating materials for buildings, bridges, and automobiles that can endure stresses.
• Manufacturing: This process shapes and molds metals into the shapes that are wanted.
• Material Selection: Based on their mechanical characteristics, materials are chosen according to their suitability for various purposes. Engineers and scientists can select the appropriate materials for a range of applications by examining this curve, guaranteeing the effectiveness and safety of machines and buildings.
Note:-
Variation in Elasticity:-
(i) Effect of temperature
In general elasticity decreases as the temperature increases.
On annealing i.e on alternate heating and cooling, elasticity decreases.
(ii) Effect of impurities
If the impurity is more elastic, the elasticity of the material increases.
If the impurity is more plastic (less elastic), the elasticity of material decreases.
Elastic Relaxation Time:-
The time delay in restoring the original form after removal of deforming force is called elastic
For phosphor, bronze, silver and gold, the time is negligibly small.
For quartz, it is minimum and for glass, it is high.
A graphical depiction of a material’s deformation under stress is the stress-strain curve. It aids in understanding the mechanical characteristics of a material and illustrates the connection between stress (force per unit area) and strain (deformation).
The stress-strain curve has several regions:
Proportional Limit – Follows Hooke’s Law (stress is proportional to strain).
Elastic Limit – The maximum point up to which the material can return to its original shape.
Yield Point – The material begins permanent deformation.
Plastic Region – The material deforms without breaking.
Ultimate Strength (Point – The maximum stress the material can withstand.
Fracture Point – The material breaks.
1 thought on “Stress-Strain Curve”